Charting the Course to Decarbonization in Manufacture of metal structures and parts of structures: Strategies and Initiatives
This article explores strategies and initiatives for reducing carbon emissions in the manufacture of metal structures and parts, in order to achieve decarbonization.
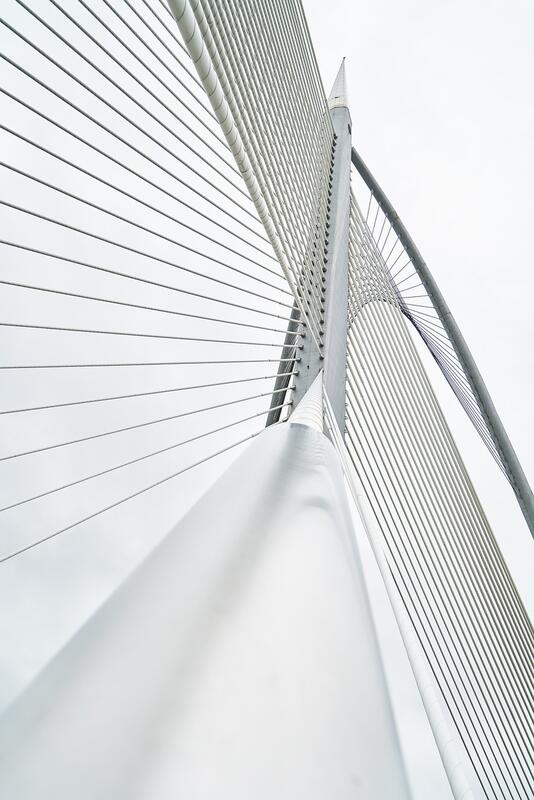
The manufacture of metal structures and parts of structures is a vital sector of the economy, providing essential components for construction, transportation, and other industries. However, like many other industries, it is also a significant source of carbon emissions, contributing to the global climate crisis. Decarbonisation of this sector is therefore essential to mitigate the impacts of climate change and transition to a sustainable future.
What is Decarbonisation in the Manufacture of Metal Structures and Parts of Structures Sector and Why is it Important?
Decarbonisation refers to the process of reducing or eliminating carbon emissions from a particular sector or activity. In the context of the manufacture of metal structures and parts of structures, decarbonisation involves reducing the carbon footprint of the production process, including the use of energy, raw materials, and transportation.
Decarbonisation is important for several reasons. Firstly, the manufacture of metal structures and parts of structures is a significant source of carbon emissions, accounting for around 7% of global greenhouse gas emissions. This sector is particularly challenging to decarbonise due to the high energy requirements of the production process, the use of fossil fuels, and the reliance on raw materials with high carbon footprints.
Secondly, the manufacture of metal structures and parts of structures is a critical sector for the global economy, providing essential components for construction, transportation, and other industries. Decarbonisation of this sector is therefore essential to ensure a sustainable future and avoid the worst impacts of climate change.
What are the Main Sources of Carbon Emissions in the Manufacture of Metal Structures and Parts of Structures Sector?
The manufacture of metal structures and parts of structures is a complex process that involves several stages, each of which contributes to carbon emissions. The main sources of carbon emissions in this sector include:
- Energy use: The production of metal structures and parts of structures requires a significant amount of energy, which is typically generated from fossil fuels. The use of fossil fuels is a significant source of carbon emissions, accounting for around 70% of total emissions in this sector.
- Raw materials: The production of metal structures and parts of structures requires raw materials such as iron ore, coal, and limestone, which have high carbon footprints. The extraction, processing, and transportation of these materials contribute to carbon emissions.
- Transportation: The transportation of raw materials, finished products, and equipment also contributes to carbon emissions. The use of fossil fuel-powered vehicles for transportation is a significant source of emissions in this sector.
- Waste and by-products: The production process generates waste and by-products, which can also contribute to carbon emissions. For example, the production of steel generates carbon dioxide as a by-product.
How Can We Reduce Carbon Emissions in the Manufacture of Metal Structures and Parts of Structures Sector?
Reducing carbon emissions in the manufacture of metal structures and parts of structures sector requires a combination of strategies, including:
- Energy efficiency: Improving energy efficiency in the production process can significantly reduce carbon emissions. This can be achieved through measures such as upgrading equipment, optimizing processes, and using renewable energy sources.
- Use of renewable energy: The use of renewable energy sources such as solar, wind, and hydropower can significantly reduce carbon emissions in this sector. This requires investment in renewable energy infrastructure and the adoption of new technologies.
- Material efficiency: Reducing the use of raw materials and optimizing their use can also reduce carbon emissions. This can be achieved through measures such as recycling, reusing materials, and using alternative materials with lower carbon footprints.
- Transportation: Reducing the carbon footprint of transportation can also contribute to decarbonisation in this sector. This can be achieved through measures such as using electric vehicles, optimizing transportation routes, and reducing the need for transportation through local sourcing.
What are the Challenges Facing Decarbonisation in the Manufacture of Metal Structures and Parts of Structures Sector?
Decarbonisation of the manufacture of metal structures and parts of structures sector faces several challenges, including:
- High energy requirements: The production process requires a significant amount of energy, which is typically generated from fossil fuels. The high energy requirements of this sector make decarbonisation challenging.
- Raw materials: The production process relies on raw materials such as iron ore, coal, and limestone, which have high carbon footprints. Finding alternative materials with lower carbon footprints can be challenging.
- Cost: Decarbonisation requires significant investment in new technologies and infrastructure, which can be costly. This can be a barrier for companies, particularly small and medium-sized enterprises.
- Regulatory framework: The lack of a clear regulatory framework for decarbonisation can also be a challenge. Companies may be hesitant to invest in decarbonisation without clear policies and incentives from governments.
What are the Implications of Decarbonisation for the Manufacture of Metal Structures and Parts of Structures Sector?
Decarbonisation of the manufacture of metal structures and parts of structures sector has several implications, including:
- Economic opportunities: Decarbonisation can create new economic opportunities, such as the development of new technologies and infrastructure. This can create jobs and stimulate economic growth.
- Competitive advantage: Companies that invest in decarbonisation can gain a competitive advantage by reducing their carbon footprint and meeting the growing demand for sustainable products.
- Regulatory compliance: Decarbonisation may become a regulatory requirement in the future, particularly as governments take action to mitigate the impacts of climate change. Companies that invest in decarbonisation now may be better positioned to comply with future regulations.
- Environmental benefits: Decarbonisation can significantly reduce carbon emissions and mitigate the impacts of climate change. This can have significant environmental benefits, such as reducing air pollution and protecting biodiversity.
Conclusion
The manufacture of metal structures and parts of structures is a significant source of carbon emissions, contributing to the global climate crisis. Decarbonisation of this sector is therefore essential to mitigate the impacts of climate change and transition to a sustainable future. This requires a combination of strategies, including improving energy efficiency, using renewable energy sources, reducing the use of raw materials, and optimizing transportation. While decarbonisation faces several challenges, it also presents economic opportunities, competitive advantages, and environmental benefits. Decarbonisation of the manufacture of metal structures and parts of structures sector is therefore essential for a sustainable future.